Mastering Process Improvement Plans: A Detailed Overview
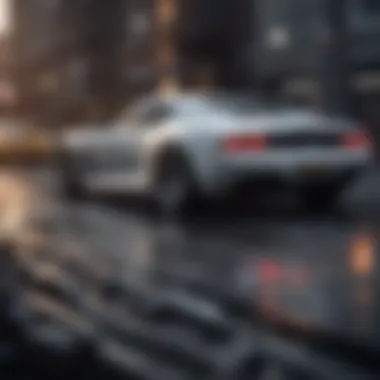
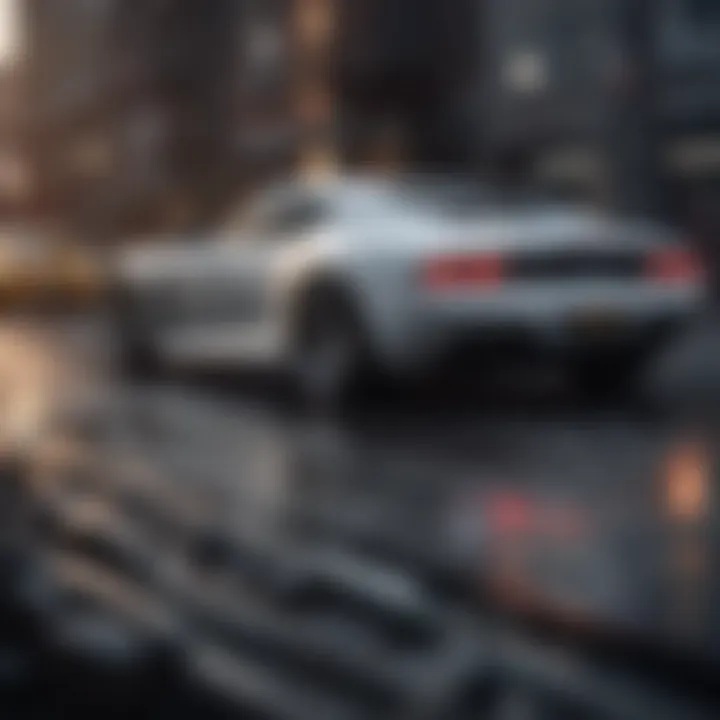
Intro
Process improvement plans are essential tools for organizations striving for growth and efficiency. These plans serve as roadmaps, guiding teams through the complexities of refining their existing processes. They are useful in identifying inefficiencies, enhancing productivity, and ultimately meeting organizational goals. This guide aims to shed light on the core components of effective process improvement plans, offering a clear understanding of the steps involved.
What is a Process Improvement Plan?
A process improvement plan details the specific actions taken to optimize a particular process within an organization. It outlines the scope, objectives, and methodologies that the team will use to identify inefficiencies. The goal is to transform these processes into more efficient, effective systems that yield better results. Understanding these elements is crucial, as it sets the foundation for successful implementation.
The Importance of Process Improvement
Organizations today face a myriad of challenges. Competition is fierce, customer expectations are high, and operational costs often seem to rise without respite. A well-structured process improvement plan acts as a critical strategy to combat these challenges. By focusing on systematic enhancements, organizations can achieve greater efficiency, reduce waste, and boost employee morale. Moreover, implementing process improvements can lead to better customer satisfaction, as services or products become more reliable and timely.
Key Components of an Effective Plan
An effective process improvement plan typically includes:
- Process Definition: Clearly outlining what the current process looks like.
- Identification of Improvements: Determining key areas where enhancements can be made.
- Implementation of Changes: Detailing how changes will be enacted and who will be responsible.
- Measurement Metrics: Establishing standards for gauging success and identifying future challenges.
By incorporating these elements, organizations can create robust plans that not only address current inefficiencies but also promote ongoing improvement.
"Improvement usually means doing something that we have never done before." – Anonymous
Identifying Improvement Opportunities
To move forward with a process improvement plan, it is crucial to conduct a thorough analysis of the existing processes. This involves collecting data, gathering employee feedback, and studying customer experiences. The identification phase often includes:
- Process Mapping: Visualizing the steps and stages within the current process.
- Data Gathering: Collecting quantitative and qualitative data that highlight inefficiencies.
- Stakeholder Feedback: Engaging with team members to gain insights into bottlenecks and frustrations.
This comprehensive approach ensures that organizations have a clear picture of their operational landscape before initiating improvements.
Implementation Challenges
Implementing a process improvement plan can pose various challenges. Resistance to change often emerges from employees who may be comfortable with the status quo. Furthermore, insufficient training and lack of buy-in from leadership can derail initiatives. To overcome these obstacles, organizations should focus on clear communication about the benefits of improvements, provide appropriate resources, and foster a culture of collaboration.
By understanding these dynamics, organizations can better navigate the complexities associated with implementing changes.
End
A well-conceived process improvement plan is vital for any organization seeking to thrive in today’s competitive environment. By focusing on defining processes, identifying improvements, and implementing effective changes, organizations can achieve substantial efficiency gains and enhance their overall performance. The insights shared in this guide aim to equip readers with the fundamental understanding necessary to embark on their own process improvement journeys.
Defining a Process Improvement Plan
Defining a process improvement plan is a critical step in enhancing operational efficiency within any organization. This section will discuss the key elements of these plans and their significance. A well-structured plan not only outlines the required improvements but also provides a roadmap for successful implementation. Emphasizing clarity in the definitions and the objectives is crucial for any managerial or operational team attempting to navigate the complexities of process management.
What is a Process Improvement Plan?
A process improvement plan is a systematic approach intended to identify, analyze, and improve existing processes within an organization. It is designed to enhance efficiency, reduce waste, and optimize overall work methods. This plan typically includes methods for gathering data, assessing performance, and identifying gaps in current processes. Documentation is also a key aspect, as it helps in tracking progress and ensuring accountability.
To be effective, the plan must be precise in detailing the targets for improvement. This clarity allows teams to align their efforts effectively. For instance, a plan may focus on improving the customer service response time or reducing the cycle time for a specific production line.
The Importance of Process Improvement
The importance of process improvement cannot be underestimated. In today’s competitive business landscape, organizations that fail to adapt or optimize their processes risk obsolescence. Here are several reasons why establishing a process improvement plan is essential:
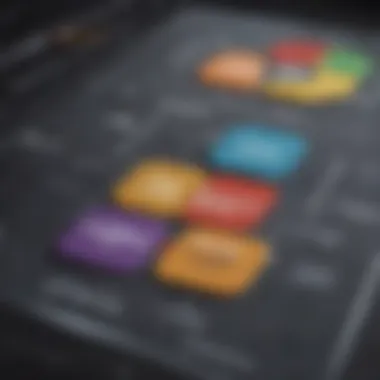
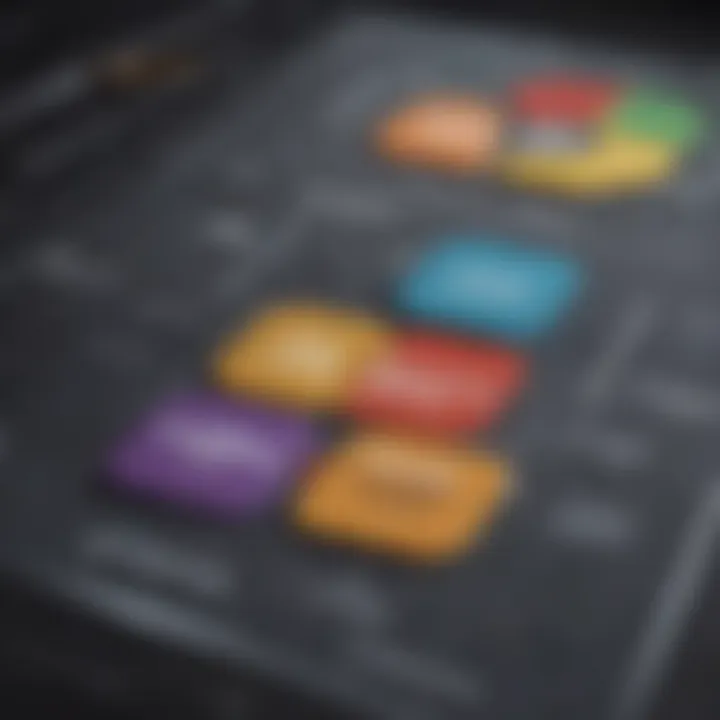
- Enhanced Efficiency: Streamlining processes reduces waste and increases productivity, enabling teams to focus on value-added activities.
- Cost Reduction: Identifying inefficiencies can lead to significant cost savings by minimizing resources spent on non-essential activities.
- Improved Quality: Consistent evaluation and refinement of processes help maintain high standards for quality, which is crucial for customer satisfaction.
- Data-Driven Decisions: Process improvement plans rely on data collection and analysis, facilitating informed decision-making.
- Agility: An organization equipped with an effective process improvement plan can adapt quickly to market changes, maintaining a competitive edge.
A well-defined process improvement plan ensures not just the identification of problems but also the ability to implement sustainable solutions.
Implementing such plans can contribute to the long-term success of an organization by fostering a culture of continuous improvement.
Key Components of a Process Improvement Plan
In the realm of process improvement, understanding core components serves as the backbone of formulating an effective plan. Key components provide structure and clarity. They empower organizations to identify specific elements requiring attention, thereby unlocking benefits such as enhanced efficiency and productivity.
Identifying the Process to Improve
The first step in any improvement plan is determining which process needs focus. Processes can span various functions: manufacturing, customer service, or even administrative tasks. To identify this, one must evaluate performance data, employee feedback, and customer satisfaction metrics. Tools like process mapping may assist in visualizing where inefficiencies lie. Prioritize processes that impact overall objectives and customer experiences.
By honing in on a particular process, organizations can direct resources effectively and align efforts with overarching goals. Doing so ensures any changes made address the areas most in need of enhancement.
Creating a Baseline for Measurement
Establishing a baseline is an essential part of the process improvement plan. This baseline reflects current performance levels. It is vital for tracking progress over time after changes are made. One must collect quantitative data, which can include cycle times, error rates, or output levels, depending on the process in question. This data allows organizations to measure the effectiveness of the improvements adopted.
In addition, qualitative assessments, such as employee surveys, can complement the quantitative data, offering insight into employee experiences with the current process. Both types of data contribute to a stronger understanding of where the starting point is before any changes are implemented.
Setting Goals and Objectives
Once the process and baseline are determined, setting specific goals and objectives is the next vital step. Goals should be SMART: Specific, Measurable, Achievable, Relevant, and Time-bound. This framework ensures they are clear and actionable. For example, instead of vaguely saying, "We want to improve efficiency," a better goal might be, "We aim to reduce the customer service response time from 12 hours to 2 hours within six months."
These objectives should align with the overall mission of the organization and consider resources available. It is important to communicate these goals across the team to foster buy-in and shared purpose. Success hinges on aligning everyone’s effort towards a common target, making clear what success looks like in more concrete terms.
Clearly defined objectives promote accountability and provide a reference point for determining progress.
Steps in Developing a Process Improvement Plan
Developing a solid process improvement plan is crucial for enhancing efficiency in any organization. Each step minimizes waste and maximizes productivity. This section outlines the various stages involved in creating a process improvement plan and illustrates the significance of each step for the overall success of the initiative.
Gathering Data and Analyzing Current Processes
Before initiating changes, understanding the present state of processes is essential. Gathering data involves collecting quantitative and qualitative information about current workflows. Techniques could include surveys, interviews, and direct observations. It is imperative to consider multiple perspectives. Collecting data ensures that the analysis reflects the reality of operations.
Data analysis can reveal strengths and weaknesses in existing processes. By employing tools like process mapping or flowcharts, organizations can visualize steps and identify bottlenecks or redundancies. This step also assists in creating a baseline for future measurements. Without a clear view of current processes, any improvement efforts might lack direction.
Identifying Areas for Improvement
Once the current processes are analyzed, it is time to pinpoint specific areas that require enhancement. Look for symptoms that signal inefficiency, such as delays, errors, and customer complaints. Focused discussions with team members can also provide insights into perceived challenges.
Utilizing a structured approach, such as the Five Whys technique, can further aid in uncovering root causes of issues. Addressing root causes rather than symptoms allows for more significant and sustainable improvements. These insights inform the decisions on which processes to prioritize for improvement.
Developing Improvement Strategies
With clear areas of improvement identified, the next step involves formulating strategies that will lead to better outcomes. Theory and practice must merge here. Solutions could range from re-engineering workflow procedures to introducing new technologies. Involving team members in this stage ensures their buy-in and fosters innovation.
Strategies should be specific, measurable, achievable, relevant, and time-bound (SMART). For instance, instead of saying,
Measuring Success in Process Improvement
Measuring success in process improvement is crucial for understanding the impact of implemented changes. Without effective measurement, it is difficult to determine if the desired outcomes have been achieved. By precisely assessing results, organizations can verify if the strategies deployed are effective. This section highlights the specific elements required to ensure an accurate evaluation.
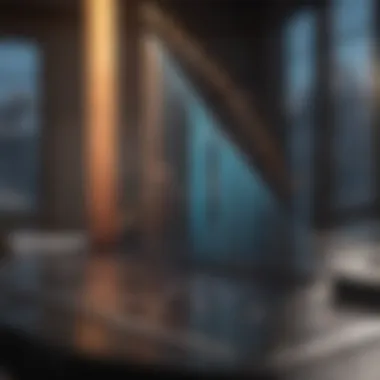
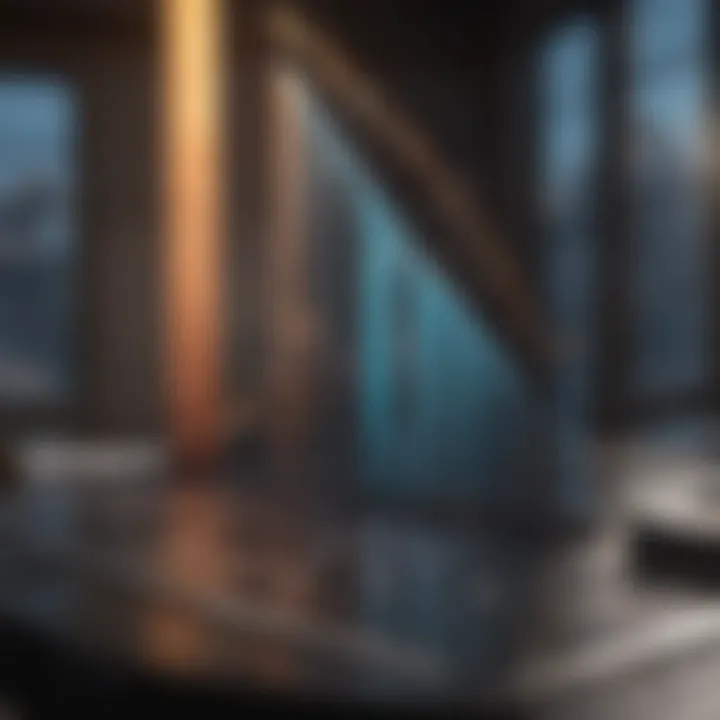
Key Performance Indicators (KPIs)
KPIs are significant in the process improvement context. These measurable values help organizations assess their success in reaching targets. Establishing relevant KPIs is a fundamental step in any improvement plan.
Some essential KPIs might include:
- Cycle Time: Measures the time taken to complete one cycle of the process.
- Error Rate: Evaluates the frequency of mistakes or defects in the process.
- Cost Efficiency: Assesses the financial performance compared to pre-improvement levels.
To identify appropriate KPIs, organizations should consider the specific goals of the improvement plan. It is important to align KPIs with organizational objectives. Ongoing monitoring of these indicators provides insights into the process performance over time.
Feedback Mechanisms
Feedback mechanisms play a vital role in measuring success. They provide ongoing insights from those directly involved with the process. Gathering feedback requires the establishment of channels for communication, such as surveys or suggestion boxes. This information can offer valuable perspectives on whether the changes are effective or need further adjustment.
Implementing mechanisms for feedback should consider the following:
- Define clear objectives for feedback to guide the process.
- Utilize various methods like interviews or focus groups to gather insights.
- Regularly analyze feedback to identify trends and areas for further improvement.
Feedback is not merely a one-time activity but a continuous cycle that informs future decisions.
In sum, selecting relevant KPIs and adopting efficient feedback mechanisms are central to evaluating process improvement efforts. These elements not only facilitate monitoring over time but also enhance the decision-making capabilities of the organization.
Challenges in Process Improvement Implementation
Implementing a process improvement plan is not just a technical exercise. It involves managing human behaviors, organizational culture, and resource constraints. Understanding these challenges is crucial for ensuring the success of the improvement initiative. By identifying and addressing these challenges, organizations can enhance their processes effectively and sustainably.
Resistance to Change
Resistance to change is one of the primary hurdles organizations face during process improvement implementation. People are often set in their ways. They may feel comfortable with existing processes, even if they are not optimal. This reluctance can stem from various factors, including fear of the unknown, lack of trust in leadership, or disbelief that the proposed changes will lead to better outcomes.
To effectively combat this resistance, organizations should communicate openly and clearly about the reasons for the change and the anticipated benefits. Involvement of employees in the change process is key. By engaging them early on, they feel a sense of ownership and responsibility toward the successful implementation of the plan.
Resource Limitations
Resource limitations pose a significant challenge for many firms attempting to implement process improvements. This includes financial resources, personnel, and time. Often, organizations are under tight budgets, making it difficult to allocate funds to necessary training or technology upgrades. Furthermore, personnel might be stretched thin, with existing workloads preventing them from fully engaging in the improvement process.
Leadership must assess available resources and plan strategically. By prioritizing critical areas for improvement, it's possible to achieve meaningful results without overstretching. Creative solutions like cross-training employees can help mitigate these limitations, leveraging existing talent more effectively.
Maintaining Momentum
Maintaining momentum once initial changes are implemented can be difficult. Organizations may experience a drop in enthusiasm after the initial excitement fades. This can lead to disengagement from the process improvement initiative and a return to old habits.
To keep the momentum alive, continuous monitoring and feedback mechanisms should be established. Regular check-ins can help reinforce commitment and provide accountability. Recognition of progress, even if small, can motivate teams to push forward and celebrate achievements. Establishing a culture of continuous improvement becomes imperative, transforming process improvement into a routine part of the organizational growth framework.
“The key to successful change is not just to implement it, but to embed it into the fabric of your organization.”
Example of a Process Improvement Plan
A well-structured example of a process improvement plan serves as a foundational tool for organizations aiming to boost efficiency and effectiveness. This section explores the significance of having a concrete example, enabling practitioners to visualize strategies and outcomes in a real-world context. When organizations undertake process improvement, seeing a clear case can assist in understanding the pathways taken, the strategies deployed, and the results generated. This detailed analysis also showcases the iterative nature of process improvement, helping teams learn and adapt along the journey.
Case Study Overview
In this case study, we will examine the process improvement plan implemented by a mid-sized manufacturing company, ABC Corp. This organization faced declining product quality and increased production costs. The leadership team recognized that without changes, their market position and profitability would suffer. They decided to focus on streamlining operations and improving quality control. The plan was designed to address these specific issues by setting measurable goals, engaging employees, and applying data-driven methodologies.
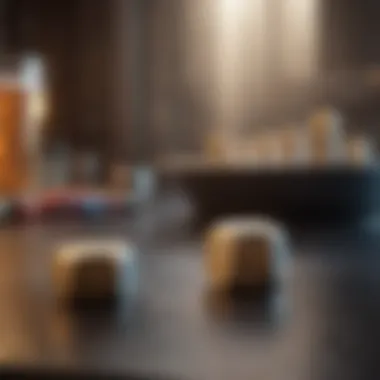
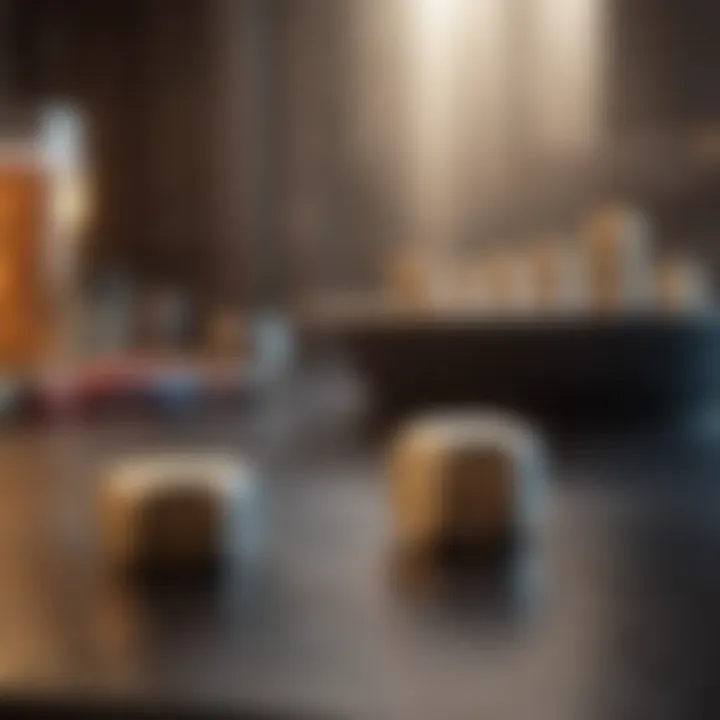
Step-by-Step Breakdown of the Plan
- Identification of Current Processes
The first step required the team to map out existing production processes. This mapping exercise revealed inefficiencies, such as excessive steps in quality checks that often delayed production. - Establishing a Baseline
To assess improvements, a baseline of current quality metrics was created. This included tracking defect rates and production cycle times over a determined period. - Setting Specific Goals
The team aimed to reduce defects by 20% within six months. Additionally, they sought to improve cycle time by 15%. - Developing Improvement Strategies
Key strategies included retraining employees on quality standards, adopting new technologies for quality monitoring, and redesigning workflow processes to eliminate bottlenecks. - Implementing Changes
Changes were rolled out in phases to minimize disruptions. Employees received training in new practices, and specific metrics were monitored closely. - Reviewing and Adjusting
Regular review meetings were scheduled every month to discuss progress, address challenges, and adjust the strategies when necessary. Feedback from team members was vital in this phase.
Results and Learnings
After the six-month implementation phase, ABC Corp. achieved significant improvements. Defect rates decreased by 25%, exceeding the original goal, while cycle times improved by 18%. These tangible results not only improved product quality but also enhanced employee morale as they witnessed the positive impact of their efforts.
Continuous assessment and adaptation of the plan were key to success.
This case highlighted the importance of stakeholder engagement at all levels. Solutions became more effective when team members felt involved in the process. Additionally, it showed that setting realistic and measurable goals is critical in ensuring motivation and focus.
This example emphasizes that a comprehensive process improvement plan is not only a roadmap but also a dynamic tool that evolves with feedback and changing circumstances. By learning from actual cases like that of ABC Corp., organizations can navigate their unique journeys toward continuous improvement.
Best Practices for Process Improvement
In order to develop an effective Process Improvement Plan, it is essential to establish a set of best practices. These practices serve as guiding principles that enhance the probability of success and efficiency in improvement initiatives. The main focus is to create a structured approach that incorporates stakeholder input, leverages technology, and promotes continuous learning. Following best practices can lead to better decision-making, greater efficiency, and higher satisfaction within the organization.
Engaging Stakeholders
Engaging stakeholders in the process improvement journey is critical. Each individual involved brings unique perspectives, skills, and insights that can significantly influence the outcome of the plan. When stakeholders are actively involved, they are more likely to support change and adapt to new processes.
To effectively engage stakeholders, consider the following:
- Identify Key Stakeholders: Determine who will be impacted by the process changes. This includes employees, management, and possibly clients.
- Communicate Clearly: Provide stakeholders with thorough information about the process improvement objectives and their roles in the development.
- Foster Collaboration: Organize workshops or meetings where stakeholders can contribute ideas and feedback. This collaborative effort can lead to innovative solutions.
Engaging stakeholders not only enhances the quality of the process improvement plan but also builds trust and buy-in across the organization.
Utilizing Technology and Tools
Technology is a pivotal aspect in the implementation of process improvement plans. Modern tools can improve efficiency, streamline operations, and provide valuable data for analysis. By integrating the right technology, organizations can monitor processes closely and manage changes more effectively.
Consider the following tools:
- Project Management Software: Tools like Asana or Trello can help in planning and monitoring progress.
- Data Analysis Tools: Software such as Tableau or Excel can visualize and analyze process data, aiding in decision-making.
- Automation Tools: Solutions like Zapier can automate repetitive tasks, allowing team members to focus on higher-priority jobs.
Incorporating these technologies helps to track performance metrics, assess improvement impacts, and maintain communication among team members.
Continuous Learning and Adaptation
Continuous learning and adaptation are essential for sustainable process improvement. The landscape of business is always changing, and organizations that are rigid may struggle to keep up. By fostering a culture of learning, organizations remain flexible and responsive to new challenges and opportunities.
Some way to encourage continuous learning:
- Regular Training Sessions: Host workshops and training to keep staff updated on new processes and technologies.
- Feedback Loops: Establish mechanisms for employees to provide ongoing feedback on new processes, so adjustments can be made when necessary.
- Celebrate Successes and Learn from Failures: Recognize achievements to motivate the team and view mistakes as a chance to grow and improve.
Adapting to feedback and lessons learned from successes and challenges will ensure that the process improvement plan remains relevant and effective over time.
The key to effective process improvements lies in engaging stakeholders, utilizing the right technologies, and embedding a culture of continuous learning within the organization.
Closure
In this article, we explored the significance of a Process Improvement Plan and outlined its core elements. A well-structured conclusion distills the essence of what has been discussed, reinforcing the primary benefits of understanding process improvement.
The importance of having a defined Process Improvement Plan cannot be overstated. It serves as a roadmap for organizations looking to enhance efficiency and effectiveness. By focusing on systematic change, companies can align their objectives with their operational reality. This alignment is critical in today's fast-paced business environment, where adaptability plays a crucial role.
Moreover, a Process Improvement Plan offers measurable benefits. It allows organizations to set tangible goals and track progress through carefully selected Key Performance Indicators (KPIs). This not only ensures accountability but also facilitates continuous improvement over time. Regular reviews and adjustments to the plan can lead to sustained operational success.
Key elements that merit consideration within the concluding section include:
- Reflection on Objectives: A successful Plan should encourage teams to reflect on their objectives and ensure alignment with broader organizational goals.
- Integration of Feedback: Gathering feedback at various stages can provide invaluable insights, reshaping the Plan to better meet the needs of all stakeholders.
- Sustainability: Emphasizing the need for ongoing review ensures that the Plan remains relevant and effective in a changing landscape.
Reflecting on these considerations reveals how a robust Process Improvement Plan can transform organizations. Its impact extends beyond mere efficiency gains; it can enhance employee morale and customer satisfaction as well.