Mastering Lean Six Sigma: Principles and Applications
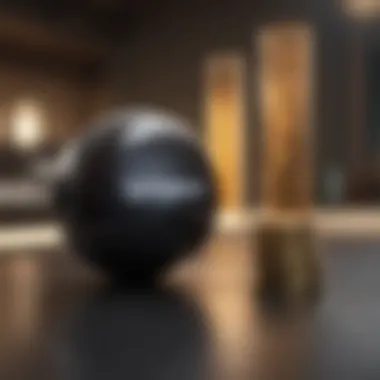
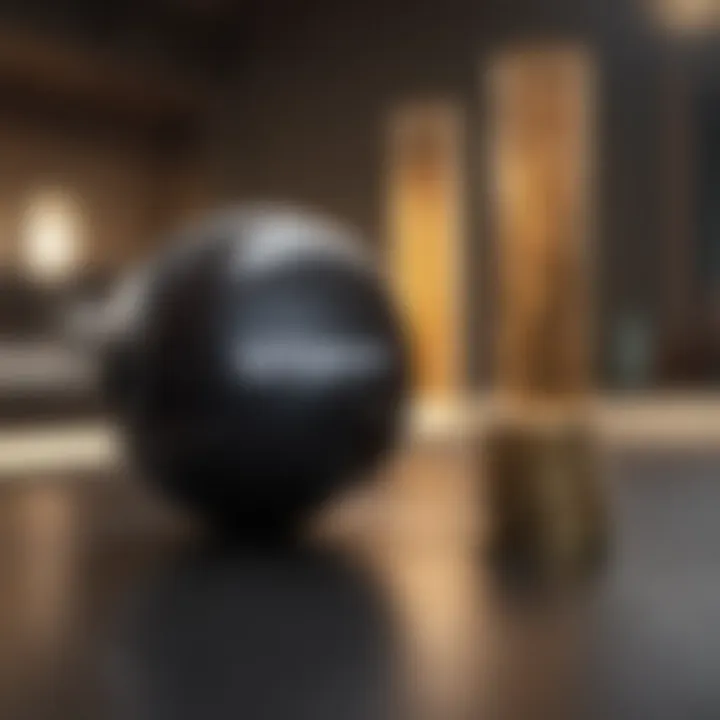
Intro
Lean Six Sigma is a methodology that combines Lean manufacturing principles and Six Sigma techniques to enhance performance by systematically removing waste and reducing variation. The genesis of these principles lies in the quest for operational excellence, where organizations strive to provide maximum value to customers while minimizing resources spent.
This comprehensive guide will take you through the essential components of Lean Six Sigma. Readers will gain insights into its origins, methodologies, and varied applications across multiple sectors. By examining real-world conversions and their impacts within organizations, the narrative will elucidate how Lean Six Sigma can streamline processes, boost efficiency, and ultimately contribute to organizational success.
Understanding Lean Six Sigma involves delving into its advantages, the challenges that might arise when integrating it into corporate culture, and the innovative tools at its disposal. The information presented here will serve as a reliable resource for investors and industry professionals aiming to make informed judgments about operational improvements and strategic investments.
Market Overview
Current Market Sentiment
The current market sentiment surrounding Lean Six Sigma reflects a growing recognition of the importance of efficiency in business operations. Many organizations have shifted towards adopting Lean Six Sigma as a standard practice, acknowledging its ability to mitigate waste and enhance productivity.
Major Indices Performance
Indices representing sectors that actively utilize Lean Six Sigma methodologies— such as manufacturing and service industries—have seen an uptick in performance metrics. This suggests that companies employing Lean Six Sigma are often better positioned to adapt to economic fluctuations compared to those that do not leverage such strategies.
Economic Indicators Analysis
Economic indicators, like productivity rates and operational cost analyses, bolster the case for Lean Six Sigma. Businesses equipped with these principles tend to report higher efficiency and lower overhead costs. Furthermore, as competition intensifies, companies realize that operational excellence can be a distinct competitive advantage.
Principles of Lean Six Sigma
The Foundations of Lean
Lean principles focus on eliminating waste within an organization’s processes. This includes identifying non-value-added activities and finding ways to eliminate them. Some of the core ideas within Lean include:
- Value is defined by the customer.
- Value stream mapping helps visualize processes.
- Waste reduction is key to improving flow.
The Core of Six Sigma
Contrasting with Lean, Six Sigma emphasizes reducing variation and improving quality. It applies statistical methods and quality management principles to refine processes. Six Sigma operates under the framework of DMAIC:
- Define
- Measure
- Analyze
- Improve
- Control
By showcasing how these methodologies work in concert, organizations can ultimately enhance quality while driving efficiencies.
Applications in Various Industries
Lean Six Sigma’s versatility allows for implementation across diverse sectors, including manufacturing, healthcare, finance, and logistics. Each of these industries encounters unique challenges but benefits exponentially from effective waste reduction and quality improvement strategies.
Manufacturing
In manufacturing, Lean Six Sigma is applied to optimize production lines. Companies use techniques like 5S and value stream mapping to achieve smoother operations.
Healthcare
Healthcare organizations focus on reducing patient wait times and enhancing service delivery through Lean Six Sigma, which directly translates to better patient care.
Financial Services
In financial services, eliminating redundant processes can significantly improve customer satisfaction and operational efficiency, which is achieved via detailed Six Sigma analyses.
“Lean Six Sigma is not merely a set of tools; it embodies a cultural shift towards continuous improvement.”
Closure
Understanding Lean Six Sigma principles is crucial for businesses looking to improve their operational frameworks. This guide not only provides a thorough understanding but sets the groundwork for deploying Lean Six Sigma methodologies effectively. The benefits of such adoption extend beyond mere efficiency; they foster a culture that values continuous improvement, ultimately leading to sustainable success.
Prelims to Lean Six Sigma
Lean Six Sigma combines two powerful methodologies: Lean manufacturing and Six Sigma. Understanding Lean Six Sigma is crucial for organizations aiming to enhance operational efficiency and deliver customer value. This section highlights its significance and foundational elements.
Lean manufacturing focuses on the elimination of waste within an organization. It strives to enhance process efficiency by reducing steps that do not add value. Businesses that adopt Lean practices usually see improvements in their lead time, cost savings, and enhanced responsiveness to customer needs.
In contrast, Six Sigma emphasizes reducing variation and improving quality through data-driven decision making. It uses statistical methods to identify and remove the causes of defects in processes. By embracing Six Sigma, companies can achieve higher quality outputs and drive better customer satisfaction.
When these two methodologies merge, the result is a comprehensive system that not only improves efficiency but also enhances quality. This integrated approach leads organizations to optimize their processes and make smarter, data-backed decisions.
Benefits of Lean Six Sigma include:
- Increased Efficiency: Streamlining processes leads to faster output and reduced resource wastage.
- Higher Quality: Focus on minimizing defects promotes customer satisfaction and loyalty.
- Employee Engagement: A culture of continuous improvement encourages team involvement and innovation.
Organizations must consider several factors when adopting Lean Six Sigma. Training is essential to equip staff with necessary tools and mantality. Leadership commitment is also vital for fostering a culture supportive of these principles.
Implementing Lean Six Sigma involves overcoming challenges such as resistance to change and misaligned goals. However, with careful planning and effective communication, organizations can extensively improve their operational functions.
Lean Six Sigma helps businesses make informed choices that lead to long-term success.
Historical Background of Lean Six Sigma
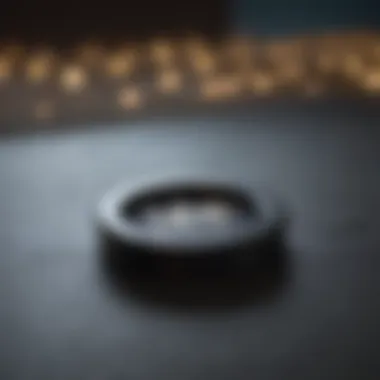
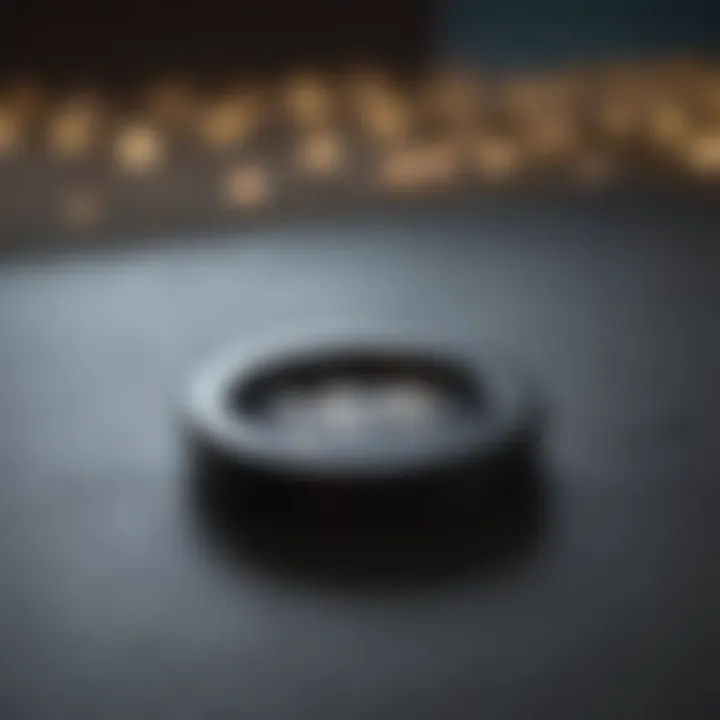
The historical background of Lean Six Sigma provides vital context for understanding its relevance in modern industries. Lean Six Sigma is not a concept that emerged overnight; rather, it represents a confluence of various methodologies developed over decades. Recognizing the origins, evolution, and integration of both Lean and Six Sigma principles can help organizations appreciate the advantages these practices offer, alongside their practical applications.
Origins of Lean Manufacturing
Lean manufacturing traces its roots to the Toyota Production System (TPS) developed in the mid-20th century. This system was mainly aimed at reducing waste and improving efficiency in manufacturing processes. The key principle of this methodology was to create value from the customer's perspective while minimizing everything that did not add value.
The approach focused on speed, efficiency, and cost reduction. For instance, Toyota's adoption of just-in-time production meant producing only what was needed, when needed. This significantly reduced excess inventory and enhanced flexibility. As a result, Lean manufacturing introduced methods such as:
- Kaizen (continuous improvement)
- Jidoka (automation with a human touch)
- Standardized work to ensure consistency
These concepts paved the way for various industries to embrace a culture centered around eliminating waste and enhancing product or service quality.
Evolution of Six Sigma
Six Sigma emerged in the 1980s, primarily at Motorola, as a response to quality control challenges. It aimed to reduce defects and improve overall process quality through statistical analysis. Motorola introduced a systematic approach to problem-solving that relied heavily on data and precise measurement techniques.
The term 'Six Sigma' refers to the goal of achieving fewer than 3.4 defects per million opportunities, emphasizing the desire for near perfection. Key methodologies included the DMAIC (Define, Measure, Analyze, Improve, Control) framework, allowing organizations to identify root causes of defects and implement effective solutions. Components critical to Six Sigma included:
- Process capability measurement
- Statistical analysis
- Customer focus and feedback
Over the years, Six Sigma gained popularity and was adopted by various sectors, including manufacturing, healthcare, and finance, demonstrating its universal applicability in improving quality and reducing costs.
Integration of Lean and Six Sigma
The integration of Lean manufacturing and Six Sigma principles marks a pivotal development in operational efficiency narratives. While Lean emphasizes speed and waste reduction, Six Sigma focuses on quality and statistical rigor. Combining these approaches creates a powerful synergy that enhances process performance on various fronts.
This integration allows organizations to:
- Drive efficiencies by eliminating waste (Lean)
- Enhance quality through data-driven decisions (Six Sigma)
As businesses began to recognize the benefits of this combination, the term Lean Six Sigma gained traction. Organizations worldwide started implementing Lean Six Sigma practices to not only improve their processes but also gain a competitive edge in their respective markets.
The unification of Lean and Six Sigma is not just about efficiency. It encourages a culture of continuous improvement and adaptation, fostering resilience in changing environments.
The historical background of Lean Six Sigma underscores the evolution of thought surrounding operational excellence. By understanding these principles, leaders can better foster environments conducive to high-performance outcomes.
Core Principles of Lean Six Sigma
Lean Six Sigma stands as a methodology built on the foundation of enhancing efficiency and quality. The core principles of this approach are designed to eliminate waste, optimize processes, and deliver value to the customer. Understanding these principles is essential for anyone looking to integrate Lean Six Sigma into their operations.
Focus on Customer Value
In Lean Six Sigma, the emphasis on customer value is paramount. This principle dictates that organizations must comprehend what their customers truly value. It involves gathering insights to understand customer expectations and preferences. By doing this, businesses can align their processes to meet these expectations effectively.
An organization that puts customer value first tends to foster loyalty and satisfaction. This can lead to increased market share, improved reputation, and ultimately, higher profits. The focus should be on delivering products and services that not only meet requirements but also exceed them whenever possible.
Reduction of Waste
Eliminating waste is another significant principle of Lean Six Sigma. Waste in a business context refers to any activities or processes that do not contribute value to the customer. This can include overproduction, unnecessary movement, delays, and defects.
Identifying and reducing waste helps streamline operations. It leads to a more efficient use of resources. An organization that actively works on waste reduction can improve productivity and decrease costs. Methods such as Value Stream Mapping can help in identifying areas where waste occurs and how to address it.
Continuous Improvement Culture
The principle of continuous improvement encourages organizations to create a culture of ongoing enhancement. This approach means that all employees, from top management to the front-line workers, should seek ways to improve their work processes continually.
By fostering a culture of improvement, organizations can react quickly to changing conditions and customer needs. Regular training and engagement are fundamental. Employees should feel empowered to suggest improvements and share their insights. This collaborative mindset can lead to innovative solutions and a more agile organization.
Data-Driven Decision Making
Data-driven decision making is critical within Lean Six Sigma. It stresses the importance of using data to guide organizational decisions. This principle requires businesses to collect relevant data accurately and analyze it appropriately. By doing so, organizations can identify problems, track performance, and gauge improvement.
Data allows for objective evaluations rather than relying on subjective opinions. With statistical tools, organizations can uncover trends and patterns that inform their strategies. This approach results in better-targeted actions and optimizations across processes.
"In a world filled with data, making decisions based on evidence is essential for success in Lean Six Sigma."
In summary, these core principles work in tandem to form the backbone of Lean Six Sigma methodologies. Each principle contributes to the ultimate goal of organizations: delivering value to customer while maintaining efficiency and quality.
Lean Six Sigma Methodologies
Lean Six Sigma methodologies are critical to understanding the framework. They provide structured approaches to problem-solving and process improvement. Both frameworks aim to minimize waste and maintain quality. Integrating these methodologies can enhance organizational efficiency.
Lean focuses on improving flow and reducing lead times, while Six Sigma concentrates on reducing process variation. This combination enables a more comprehensive view of operational efficiency. In this section, we will explore two primary methodologies: DMAIC and DFSS.
Define-Measure-Analyze-Improve-Control (DMAIC)
DMAIC is a cornerstone of Lean Six Sigma. It represents five phases which guide teams in improving existing processes. Each phase has its unique roles.
1. Define: Identify the problem, project goals, and customer requirements. Clear objectives are essential. This phase sets the foundation for successful implementation.
2. Measure: Gather data to understand the current process. Accurate data collection is crucial. It helps in assessing the performance of processes before any improvements are made.
3. Analyze: Focus on identifying root causes of defects or variations in processes. Tools such as fishbone diagrams can help. This analysis allows for targeted solutions.

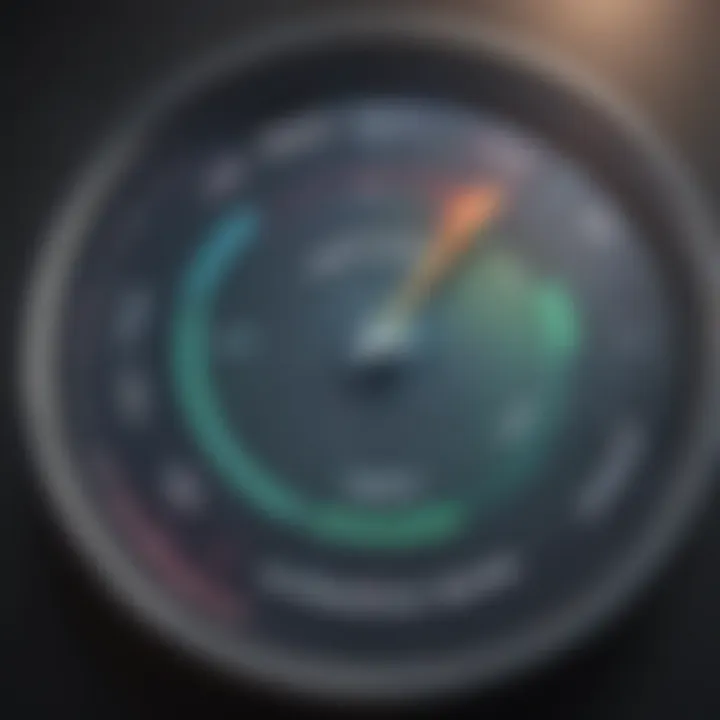
4. Improve: Develop solutions to address the identified issues. This stage tests and implements these solutions, aiming for better performance.
5. Control: Establish standard operating procedures to maintain the gains. Monitoring and control systems are essential to ensure sustainability.
DMAIC is beneficial for organizations aiming to enhance their processes systematically. It's data-driven, making it easier to authenticate the changes made.
Design for Six Sigma (DFSS)
DFSS differs from DMAIC as it focuses on designing new processes or products rather than improving existing ones. This methodology ensures that quality is built into the design from the start and avoids problems later in development.
Key Phases of DFSS:
- Define: Similar to DMAIC, it begins with defining customer needs. Understanding what the market requires is vital.
- Measure: This involves collecting metrics that will be used in the design process. These metrics are used to evaluate design performance.
- Analyze: Design alternatives are analyzed against customer needs and requirements. This examination helps in selecting the most viable design options.
- Design: Develop prototypes based on analysis. This is where creativity meets functionality.
- Verify: Test the designed product or process to ensure it meets the required specifications and customer satisfaction.
DFSS advocates for a proactive approach. It minimizes risks in the design stage, ensuring that the final product is nearer to what the customer desires.
The implementation of Lean Six Sigma methodologies can result in significant improvements in overall efficiency and quality.
Both DMAIC and DFSS are vital for Lean Six Sigma. They provide structured approaches that lead to enhanced performance, higher quality, and ultimately better customer satisfaction.
Tools and Techniques in Lean Six Sigma
Lean Six Sigma offers various tools and techniques that help organizations identify opportunities for improvement and enhance operational performance. These tools are designed to support the principles of Lean Six Sigma, ensuring that processes become more efficient while maintaining quality standards. Understanding these essential tools is crucial for anyone looking to implement Lean Six Sigma effectively. They enable teams to analyze data, visualize workflow, and problem-solve effectively.
Value Stream Mapping
Value Stream Mapping is a powerful tool used to visualize the steps in a process. It provides insights into how value flows through a system. By mapping out each step, organizations can identify areas of waste, redundancies, and inefficiencies.
Here are some key benefits of Value Stream Mapping:
- Visual Representation: It helps summarize the current state of a process visually, making it easier for team members to understand.
- Waste Identification: Users can clearly see where waste occurs in the process and highlight areas needing improvement.
- Future State Planning: It facilitates the creation of future state maps, outlining how the process should look after improvements have been made.
In short, Value Stream Mapping streamlines the path towards operational excellence and directly aligns with Lean Six Sigma’s focus on customer value.
Root Cause Analysis
Root Cause Analysis (RCA) is critical in Lean Six Sigma, as it focuses on identifying the underlying causes of problems rather than merely addressing symptoms. By understanding the root cause, organizations can target their efforts effectively to prevent issues from recurring.
Key aspects of Root Cause Analysis include:
- Methodologies: Various methodologies exist for conducting RCA, including the 5 Whys, Fishbone Diagrams, and Pareto Analysis.
- Proactive Problem Solving: Identifying root causes shifts the focus from reactive to proactive problem-solving.
- Sustainable Solutions: Solutions derived from RCA are usually more sustainable, as they address the crux of the problem.
Hence, applying Root Cause Analysis in Lean Six Sigma processes enhances quality and reduces the likelihood of defects or inefficiencies.
Statistical Process Control (SPC)
Statistical Process Control is another essential technique in Lean Six Sigma that uses statistical methods to monitor and control a process. By understanding variations within processes, organizations can ensure that they remain within specified limits and maintain quality standards.
Benefits of SPC include:
- Real-Time Monitoring: SPC allows operations to track performance in real-time, helping to identify trouble spots before they escalate into more significant issues.
- Data-Driven Insights: It promotes data-driven decision-making by providing visual representations of process variations.
- Improvement Measurement: Organizations can measure the effect of improvements and variations consecutively.
Understanding and implementing these tools can significantly elevate an organization’s Lean Six Sigma efforts. Each tool serves a specific purpose, yet when combined, they can create a robust framework for sustained operational excellence.
Benefits of Implementing Lean Six Sigma
Implementing Lean Six Sigma can have profound impacts on an organization's operations and overall performance. Companies increasingly recognize the importance of streamlining processes, minimizing waste, and ensuring high quality. This section examines the specific benefits that arise from applying Lean Six Sigma methodologies in various sectors.
Operational Efficiency
Lean Six Sigma emphasizes improving operational efficiency, which is vital for maintaining competitiveness. By systematically analyzing processes, organizations can identify bottlenecks and inefficiencies. The methodologies focus on eliminating non-value-added activities, leading to more streamlined workflows.
For instance, value stream mapping can visually depict processes and highlight areas needing improvement. It helps teams recognize which activities add value and which do not.
Operational efficiency leads to faster turnaround times and better resource utilization.
Utilizing Lean Six Sigma can enhance cycle times. Businesses often find that reducing wasted time and resources not only improves output but also boosts employee morale. When individuals see their work translate into tangible results, it fosters a culture of accountability and pride.
Cost Reduction
The aspect of cost reduction is intrinsically linked to Lean Six Sigma practices. By minimizing waste through ongoing improvement efforts, organizations often realize significant savings. Reductions in material waste, operational downtime, and rework can lead to lower costs.
A focus on data-driven decision-making also plays a role here. Companies can identify trends and areas where they can cut costs without sacrificing quality. For example, a manufacturing firm implementing Statistical Process Control (SPC) may not only observe defects in production but also reduce unnecessary expenses associated with excess inventory and quality audits.
- Cost reduction strategies might include:
- Implementing Just-In-Time inventory systems to reduce carrying costs.
- Streamlining supplier relations to better manage materials used in production.
Enhanced Quality
Quality improvement is perhaps one of the most celebrated benefits of Lean Six Sigma. By establishing a culture centered on continuous improvement, organizations can monitor and enhance product or service quality closely. This focus builds customer satisfaction, trust, and brand loyalty.
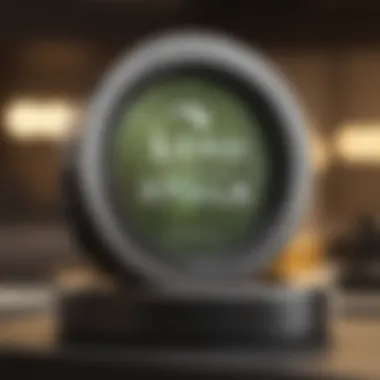
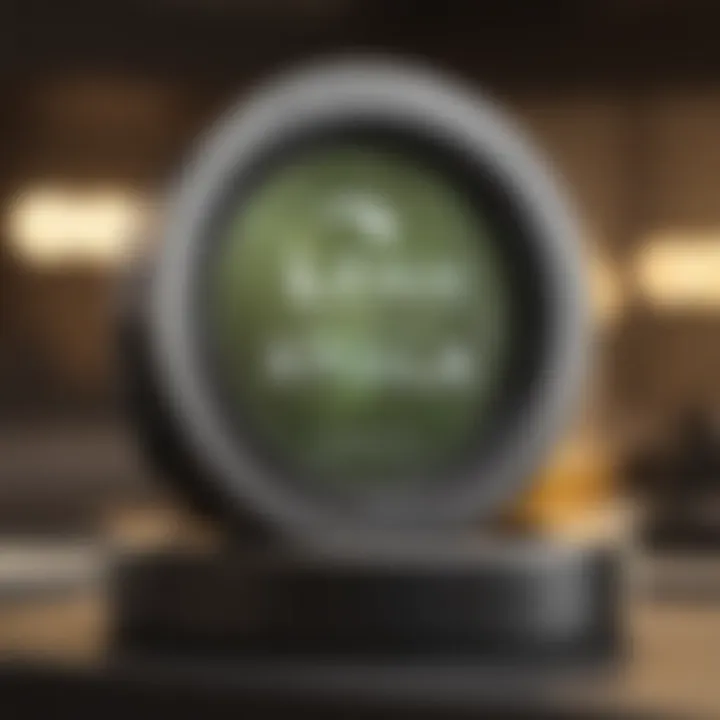
Through methodologies like DMAIC (Define-Measure-Analyze-Improve-Control), companies can gather data about defects, understand root causes, and implement solutions. The goal is not only to fix problems but to develop processes that prevent defects from occurring in the first place.
Enhancing quality might involve:
- Regular training and development for employees to keep them informed on the best practices.
- Implementing feedback mechanisms to capture customer insights promptly.
Ultimately, the integration of Lean Six Sigma principles result in products and services that meet or exceed customer expectations, which can differentiate a company in competitive markets.
Challenges in Lean Six Sigma Adoption
Adopting Lean Six Sigma (LSS) brings about significant benefits, but organizations often face challenges that can hinder its success. Understanding these challenges is essential for making informed decisions regarding implementation strategies. Resistance to change and misalignment with organizational goals are critical factors that can impede the effectiveness of Lean Six Sigma initiatives.
Resistance to Change
Resistance to change is a common phenomenon in any organization. Employees may feel threatened by new methods or processes introduced by Lean Six Sigma. This resistance can stem from a lack of understanding or fear of job security. To address this, effective communication is key. Organizations need to clearly convey the benefits of Lean Six Sigma, not just for the company but also for the individuals involved.
- Training and Education: Providing comprehensive training can reduce uncertainty. Employees should feel equipped to tackle new processes confidently.
- Engagement: Involving employees in the planning phase promotes ownership. When workers understand their role in the change, they are more likely to embrace it.
- Leadership Support: Leaders must champion Lean Six Sigma initiatives. Their commitment sets the tone for the rest of the organization.
“A change in process requires a change in mindset.”
Misalignment with Organizational Goals
Misalignment with organizational goals can also obstruct the successful adoption of Lean Six Sigma. Each initiative should align with the broader business objectives. When Lean Six Sigma projects do not correspond with organizational priorities, it leads to wasted resources and effort.
- Strategic Alignment: To ensure alignment, it is crucial for teams to understand the company's vision and objectives. Continuous communication between all levels of management supports this understanding.
- Measuring Success: Establishing clear performance metrics that reflect both Lean Six Sigma objectives and organizational goals aids in assessing the effectiveness of initiatives.
- Feedback Mechanisms: Regularly soliciting feedback allows for adjustments to keep projects aligned with shifting organizational goals. This iterative process fosters resilience.
Case Studies: Success Stories of Lean Six Sigma
Case studies illustrate the practical impact of Lean Six Sigma principles across various industries. They provide valuable insights into how organizations can successfully implement these methodologies. Learners and investors can see theories put into practice, highlighting real-world applications.
The significance of case studies cannot be understated. They help demonstrate the tangible benefits that stem from Lean Six Sigma initiatives. By analyzing successful practices, current and future practitioners can gather insights. This can drive optimization strategies and enhance performance metrics within their organizations.
Manufacturing Industry
The manufacturing sector serves as a prime example of Lean Six Sigma's efficacy. One notable case is the implementation at General Electric. They adopted Lean Six Sigma to address inefficiencies in their production lines. By focusing on data-driven processes, they managed to reduce defects and improve overall quality. As a result, General Electric reported significant cost savings and productivity gains.
Another illustrative case involves Ford Motor Company. By integrating Lean Six Sigma, Ford transformed its manufacturing operations. They prioritized waste elimination in production processes, which led to shorter lead times and increased throughput. This resulted not only in operational excellence but also in enhanced customer satisfaction. These examples showcase how Lean Six Sigma drives significant improvements in the manufacturing landscape.
Healthcare Sector
In healthcare, Lean Six Sigma has also made profound impacts. The Virginia Mason Medical Center in Seattle provides a compelling case. They adopted the principles to refine their patient care processes. The result was a noticeable decrease in patient wait times and increased overall satisfaction scores. By emphasizing workflow efficiency, healthcare teams enhanced service delivery.
Another success story is from the Cleveland Clinic. By utilizing Lean Six Sigma tools, they streamlined their surgical scheduling processes. This initiative led to improved resource utilization and reduced operational costs. Both cases exemplify how Lean Six Sigma methodologies can enhance patient outcomes while optimizing resource management.
These case studies underline the adaptability of Lean Six Sigma across diverse sectors. They emphasize performance improvements achievable through disciplined methodology adoption.
Future Trends in Lean Six Sigma
Understanding the future trends in Lean Six Sigma is crucial for companies that aim to maintain their competitive edge. Lean Six Sigma has already shown its value in improving processes and reducing waste. However, staying informed about the latest developments and adaptations requires attention to the elements that shape its future. This section discusses how digital transformation and the integration with agile practices are changing the landscape of Lean Six Sigma.
Digital Transformation and Automation
The rise of digital transformation is significantly influencing Lean Six Sigma methodologies. Organizations are increasingly adopting digital tools and technologies to streamline operations. Automation, in particular, plays a key role in enhancing efficiency and eliminating manual errors.
Utilizing data analytics in real time allows businesses to identify bottlenecks sooner. Lean Six Sigma's emphasis on data-driven decision-making aligns perfectly with these advancements. Companies can use software to gather data continuously, analyze it, and implement solutions quickly. The real-time feedback loops facilitate faster iterations of improvement cycles.
Moreover, automation reduces the time required for repetitive tasks. This shift frees up human resources to focus on more strategic initiatives. When teams are not burdened with manual processes, they can apply Lean Six Sigma techniques more creatively and effectively.
Key Benefits of Digital Transformation in Lean Six Sigma:
- Enhanced data collection and analysis.
- Improved process visibility and tracking.
- Reduction of cycle times through automation.
- Increased employee engagement due to reduced mundane tasks.
Integration with Agile Practices
Another notable trend is the fusion of Lean Six Sigma with agile methodologies. Agile practices prioritize flexibility and customer feedback, complementing Lean Six Sigma's focus on value and waste reduction. This integration allows organizations to become more responsive to changes in the market.
By combining the continuous improvement framework of Lean Six Sigma with agile sprints, teams can address customer needs more efficiently. This agility enables faster delivery of services or products, which is crucial in today's fast-paced environment. Furthermore, iterative processes help organizations to regularly evaluate and refine their approaches based on real-time feedback.
Additionally, integrating Lean Six Sigma and agile practices encourages a culture of collaboration. Cross-functional teams can work together to identify problems and develop solutions more rapidly. The focus on customer value remains strong, ensuring that end results align with market demands.
Considerations for Integrating Agile and Lean Six Sigma:
- Foster a mindset of collaboration and adaptability.
- Focus on customer feedback to guide improvements.
- Encourage experimentation and quick iterations of processes.
“The synthesis of Lean Six Sigma and agile methodologies is not just about improving efficiency; it’s about enriching adaptability in a rapidly changing environment.”
Epilogue
The conclusion of this comprehensive exploration into Lean Six Sigma principles serves as a crucial wrap-up. It synthesizes the findings and discussions shared in the previous sections. Lean Six Sigma is not merely a collection of strategies; it is a dedicated mindset that fosters continuous improvement through a structured approach.
In the context of this article, understanding the conclusion is vital for several reasons:
- Clear Understanding: It brings clarity to the complexities surrounding Lean Six Sigma methodologies, emphasizing their relevance in today’s fast-paced industries.
- Strategic Relevance: The conclusion highlights how essential these principles are for operational excellence. Businesses can no longer afford inefficiencies. Lean Six Sigma principles provide a pathway to both quality enhancements and waste reductions.
- Benefit Realization: Readers can appreciate the tangible benefits derived from implementing Lean Six Sigma, such as increased customer satisfaction, higher productivity, and reduced operational costs.
Furthermore, it encourages a reflective mindset for organizations. Key elements for consideration include:
- Alignment of Lean Six Sigma initiatives with broader corporate goals.
- Importance of fostering a culture of continuous improvement across all levels.
- Maintaining engagement with empirical data, ensuring decisions are made based on facts rather than assumptions.
Successful application of Lean Six Sigma requires commitment from both leadership and staff. When embraced company-wide, it propels growth and resilience against market fluctuations.