Understanding Airport Appliance Warranty: Key Insights
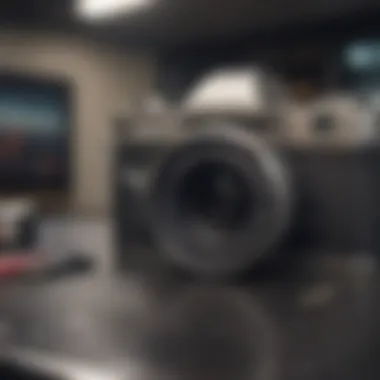
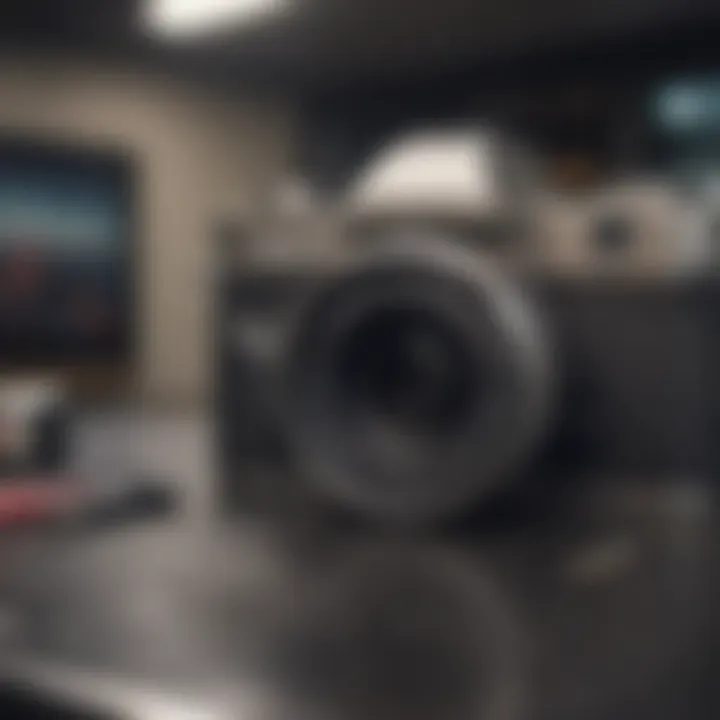
Intro
Understanding airport appliance warranties is crucial for stakeholders within the aviation sector. These warranties serve as a safety net, providing assurance concerning the durability and functionality of appliances essential for airport operations. The complexity surrounding these warranties stems from various factors including legal frameworks, coverage options, and the processes involved in claims.
In this article, we aim to demystify these complexities, ensuring that airport operators, manufacturers, and other relevant stakeholders grasp the full implications of warranty management. By dissecting the key elements that influence warranties, we will enhance informed decision-making that aligns with the operational and regulatory demands of the industry.
Market Overview
Airport appliance warranties exist in a specialized market shaped by the unique needs and challenges of the aviation industry. Understanding the current market sentiment can provide insights into how warranties are structured and perceived.
Current Market Sentiment
The sentiment around airport appliance warranties has shifted due to rising operational costs and the need for efficient equipment reliability. Stakeholders are increasingly aware of the risks associated with inadequate warranties, driving a demand for robust coverage options. Additionally, innovations in technology bring both opportunities and challenges, necessitating reevaluation of existing warranty frameworks.
Major Indices Performance
In the broader context of the aviation industry, analyzing major indices can shed light on trends that impact airport appliance warranties. Major indices reflect overall market performance and, by extension, the financial health of airport operators and equipment manufacturers. A positive performance in these indices often correlates with increased investment in high-quality appliance warranties to protect assets.
Economic Indicators Analysis
Economic indicators, such as GDP growth rates and employment statistics, play a significant role in shaping the airport appliance warranty market. When the economy thrives, airport operators are more willing to invest in comprehensive warranty protections, ensuring operational continuity. Conversely, during downturns, budget constraints might result in a more cautious approach to warranty acquisitions.
Legal Frameworks
Navigating the legal landscape surrounding airport appliance warranties is paramount. There are various laws and regulations that govern warranties, which include aspects such as consumer rights, manufacturer obligations, and warranty enforceability. Proper understanding of these legal frameworks will be discussed further, allowing stakeholders to navigate this territory effectively.
Warranty Coverage Options
Different warranties offer varying levels of coverage. Understanding these options is essential for making informed decisions.
- Standard Warranty: Basic coverage for defects found in materials and workmanship.
- Extended Warranty: Additional coverage that safeguards against a wider range of issues for a longer duration.
- Performance Warranty: Guarantees that the equipment will function according to specific performance metrics.
By examining these options, stakeholders can align their warranty choices with operational requirements, ensuring adequate protection against unforeseen failures.
Claims Process & Best Practices
Engaging with the warranty claims process can often be complex. Stakeholders need to be familiar with the steps involved.
Important Note: Keeping detailed records is essential when making warranty claims. Documentation of appliance usage, maintenance, and any issues faced can significantly influence the success of a claims process.
Implementing best practices for managing warranties will be essential for minimizing risks and maximizing benefits. This includes regular reviews of warranty terms and conditions, as well as an understanding of important timelines and stipulations.
Culmination
In summary, understanding how airport appliance warranties function is integral to effective risk management in the aviation sector. By grasping the nuances of market sentiment, legal frameworks, coverage options, and claims processes, stakeholders can make informed decisions that protect their investments. This structured understanding creates a solid foundation for navigating the increasingly complex challenges within the aviation warranty landscape.
Prologue to Airport Appliance Warranty
In the realm of aviation, the importance of airport appliance warranties cannot be overstated. They serve as a safeguard for airport operators and manufacturers alike, ensuring that critical equipment is protected against unforeseen failures. These warranties play a significant role in managing operational risks, contributing to efficiency, and optimizing maintenance strategies. Understanding what these warranties entail is crucial for stakeholders in the airport industry, as they can affect both costs and regulatory compliance.
Definition and Importance
An airport appliance warranty is a formal assurance provided by manufacturers that covers repairs or replacements of certain equipment due to defects or malfunctions. The coverage can range from parts and labor to complete equipment replacements, depending on the specific terms outlined.
The significance of these warranties lies in their ability to mitigate financial risk. They provide airport operators with peace of mind, reducing the likelihood of unexpected expenses related to equipment failure. Additionally, warranties ensure that equipment operates at optimal performance levels, which is critical in a high-stakes environment such as an airport. This can lead to improved safety, enhanced passenger experience, and overall operational reliability.
Historical Context
The concept of warranties in aviation equipment dates back several decades, evolving as technology has advanced. Initially, warranties were basic and often limited in scope, covering only the most obvious defects. However, with the growing complexity of airport appliances and the increasing reliance on advanced technology, warranties became more comprehensive.
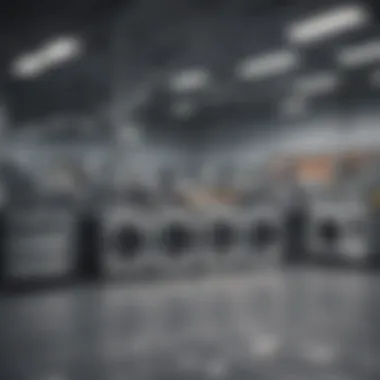
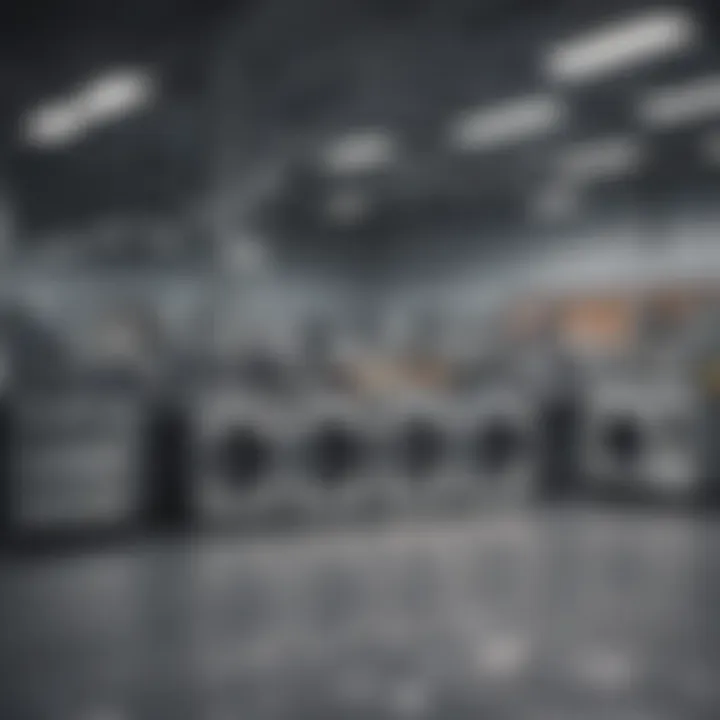
Over time, the aviation industry recognized the necessity of robust warranty frameworks to assure quality. Regulatory bodies began to set standards that required manufacturers to provide clearer and more extensive warranty information. This has led to the establishment of warranty guidelines that benefit both manufacturers and airport operators by promoting transparency and accountability in equipment maintenance.
By learning about the history and progression of airport appliance warranties, stakeholders can better appreciate their current structure and the importance of comprehensive warranty agreements. With a thorough understanding of these elements, airport operators can make informed decisions that enhance operational efficiency and compliance.
Types of Airport Appliances Covered
Understanding the types of airport appliances that come under warranty is crucial for stakeholders involved in airport operations. Each category of appliances serves a specific function that supports day-to-day airport activities. The relevance of these warranties extends beyond mere equipment repair. They represent a safeguard against financial loss, ensuring operational continuity. A thorough understanding of these categories facilitates informed decision-making and enhances warranty management strategies.
Ground Support Equipment
Ground support equipment (GSE) includes a variety of vehicles and devices that aid in the servicing of aircraft. This encompasses tugs, fuel trucks, baggage carts, and more. The reliability of GSE is vital, as delays or malfunctions can easily lead to substantial operational interruptions and financial implications.
The warranty for ground support equipment typically covers parts and labor for a defined period. This means that when an appliance fails, the airport operator can rely on the manufacturer to provide necessary repairs without incurring hefty costs. Factors such as regular maintenance routines and proper usage conditions also play a significant role in keeping warranties valid. Therefore, understanding warranty specifics helps ensure equipment longevity and operational efficiency.
Baggage Handling Systems
Baggage handling systems are integral to smooth airport operations. These systems provide the logistics needed to transport passenger luggage from check-in to the aircraft and vice versa. Any disruption in these systems can lead to lost or delayed baggage, resulting in dissatisfied passengers.
Warranties for baggage handling systems can vary in scope and coverage. It often includes provisions for both mechanical and electronic components. These warranties are essential because they protect against unexpected system failures, which can be costly. Knowing the types of coverage available allows airport operators to budget effectively and plan maintenance schedules that align with warranty conditions, ensuring that system performance is always optimal.
Passenger Boarding Bridges
Passenger boarding bridges are critical for aircraft boarding and deplaning, providing a seamless transition for passengers. They must function correctly and safely, and any technical difficulties can disrupt flight schedules.
Warranties for passenger boarding bridges generally cover structural and functional aspects. These warranties are vital in maintaining safety standards and operational integrity. Airport operators must be aware of exclusions or limitations within the warranty, as improper use can void the coverage. Thus, keeping detailed records of usage and maintenance can support claims processes when needed.
Clear understanding of warranty coverage for each type of airport appliance ensures that operators can minimize disruptions and enhance service quality.
Key Components of an Airport Appliance Warranty
Understanding the key components of an airport appliance warranty is essential for airport authorities, manufacturers, and service providers. These components dictate both the extent and limits of protection for critical aviation infrastructure. A thorough grasp of these elements can lead to more effective warranty management, ensuring that stakeholders can make informed decisions that align with operational needs.
Coverage Scope
Coverage scope defines what is included in the warranty. This can encompass parts, labor, and sometimes service for airport appliances. For instance, ground support equipment might have coverage that specifically caters to engines, hydraulic systems, and electronic components.
- Parts Covered: Often, warranties will explicitly list individual components as covered. Not all parts may be included, so understanding the specifics is critical.
- Labor Provisions: Many warranties also cover the labor required for repairs. It's vital to verify if there are hourly limits or specific service providers that can be used.
- Service Options: Some warranties include on-site service, while others may require sending equipment to a service location. This can greatly affect downtime.
A clear and comprehensive warranty can minimize risks associated with equipment failure, allowing airport operations to continue smoothly. Additionally, it provides transparency and peace of mind to the stakeholders involved.
Duration and Limitations
Duration of a warranty is another key component. This detail informs stakeholders how long the coverage will last and under what conditions it remains valid.
- Timeframe: Warranties can range from short-term spans, like one year, to extended terms that offer protection for several years.
- Renewal Terms: Some warranties allow for renewals. Understanding renewal options can prolong protection and save costs on repairs.
- Performance Metrics: Often, warranties will set limitations based on performance metrics. If equipment is misused or fails to meet operational standards, claims may be invalidated.
Analyzing these aspects is crucial for identifying what level of coverage will best minimize operational risks and enhance productivity.
Exclusions and Exceptions
A comprehensive understanding of exclusions and exceptions is paramount for managing any warranty effectively. This section delineates what is not covered under the warranty, which can often lead to misunderstandings.
- Common Exclusions: It is common for warranties to exclude coverage for issues arising from normal wear and tear, negligence, or unauthorized modifications. Knowing these exclusions can refine maintenance practices.
- Environmental Factors: Warranties may also specify that damage due to extreme environmental conditions, such as floods or earthquakes, is not covered. This is significant for airports located in certain geographic areas.
- Specific Modifications: Any unauthorized changes made to equipment can void warranties. Stakeholders must be aware of these limits to ensure compliance.
Understanding exclusions allows for better strategic planning and risk mitigation when dealing with airport appliances.
In summary, grasping the key components of warranties allows stakeholders to navigate their intricacies confidently. This knowledge not only ensures compliance but also creates opportunities for improved operational efficiency and reduced risks.
Legal Aspects of Airport Appliance Warranties
Understanding the legal aspects of airport appliance warranties is crucial for both manufacturers and airport operators. These warranties play a key role in mitigating risks associated with equipment malfunctions and failures. Legal protection helps to define responsibilities, thereby promoting accountability and trust among stakeholders. Moreover, knowing the legal framework surrounding warranties provides clarity on how to handle disputes and manage expectations.

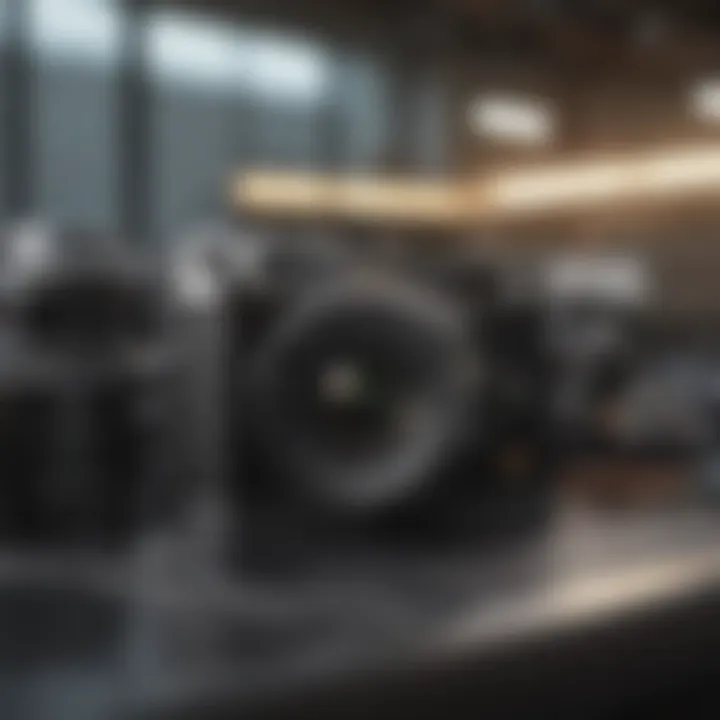
Regulatory Framework
Airport appliances are subject to various regulations that dictate warranty terms. These regulations ensure safety and reliability, which is of utmost importance in the aviation industry. Agencies, such as the Federal Aviation Administration (FAA) in the United States, set standards that equipment must meet before it's certified for use. Compliance with these regulations is crucial not only for the validity of warranties but also for the operational safety of the airports.
- Standards and Safety: Ensure that all airport appliance warranties conform to the required safety and quality standards set by governing bodies.
- Documentation: Proper documentation of compliance is necessary as it supports warranty claims.
Understanding these regulations helps in crafting warranties that meet both legal and operational requirements, ultimately impacting service delivery in an airport setting.
Enforcement and Compliance
Enforcement of warranty clauses is essential for maintaining the integrity of warranty agreements. Stakeholders must understand the processes involved in ensuring compliance.
- Claim Procedures: It is important for manufacturers to establish clear procedures for filing warranty claims. This makes it easier for operators to navigate challenges when issues arise.
- Legal Recourse: In instances of non-compliance, operators have the right to seek legal recourse. Knowing the rights and obligations of both parties protects them from potential losses.
Legal obligations surrounding warranties create a framework that assists both manufacturers and operators in resolving disputes effectively while minimizing operational disruptions.
Filing a Warranty Claim
Filing a warranty claim is a critical process in managing airport appliance warranties. This section provides insights on how to effectively navigate the complexities involved. Understanding the claim process can significantly impact operational continuity. When an appliance requires servicing or replacement, filing a warranty claim can lead to reduced financial burden and less downtime.
Initial Steps and Documentation
To initiate a warranty claim, specific steps and comprehensive documentation must be observed. First, it is essential to review the warranty agreement to identify applicable coverage and conditions. Gathering all relevant data is crucial, which typically includes:
- The original purchase invoice
- Warranty documentation
- Serial numbers of the appliances
- Detailed description of the issue
- Any prior maintenance records
- Photographic evidence of damage, if applicable
Once compiled, this documentation aids in substantiating the claim. Ensure all information is accurate to avoid unnecessary delays. It may also be beneficial to contact the manufacturer or warranty provider directly for guidance on the process.
Common Challenges
Filing warranty claims is not without difficulties. Stakeholders often encounter various challenges that can complicate the process. Among the most frequently faced challenges are:
- Document Incompleteness: Missing documents or incomplete information can lead to rejections. This emphasizes the need for thorough record keeping.
- Misunderstanding of Coverage: Warranty agreements can be intricate. Misinterpretation can result in improperly filed claims or denial of claims.
- Timeliness: Some warranties have specific timeframes for claims. Missing deadlines can jeopardize a claim.
- Manufacturer Response: Companies may have different practices regarding the review and approval of claims. A slow response can prolong resolution times, impacting operations.
- Disputes and Appeals: In cases where claims are denied, stakeholders must navigate dispute resolution processes, which can be time-consuming.
In summary, while filing a warranty claim is essential for effective warranty management, understanding the process and addressing common challenges is crucial. Stakeholders should aim to create efficient systems for documentation and monitor compliance with warranty terms to enhance the likelihood of successful claims.
It is vital to understand both the intricacies of the warranty and what documentation is necessary to support the claim effectively.
Best Practices for Warranty Management
Effective warranty management is critical in the aviation industry, particularly for airport appliances. A systematic approach to managing warranties can lead to significant improvements in operational efficiency, cost savings, and risk mitigation. It allows airport operators and manufacturers to ensure equipment reliability, maintain service levels, and manage expenses intelligently. Here are key aspects to consider in warranty management:
Record Keeping
Accurate record-keeping is foundational in warranty management. Maintaining detailed records simplifies tracking warranties and assists in filing claims. It is essential to document relevant information at each stage of the appliance’s lifecycle. This includes:
- Purchase dates: Knowing when equipment was acquired helps establish warranty timelines.
- Invoices and payment receipts: These documents serve as proof of purchase and are often required during claims.
- Service history records: Keeping detailed records of maintenance and repairs performed can also influence warranty claims. Any repairs made should be documented to provide clarity on the equipment’s condition.
Regular audits of these records are also necessary. They ensure compliance with warranty terms and help identify any gaps or discrepancies in documentation, which can hinder the claims process.
Training and Awareness
Investing in training for staff involved in warranty management is another strong practice. A knowledgeable team can better manage warranties, understand claim processes, and enforce compliance with warranty terms. Key points to focus on include:
- Understanding warranty terms: Staff should be trained to interpret warranty policies, specifically coverage scope, exclusions, and limitations.
- Claim procedures: Training personnel on the steps to file a warranty claim, including required documentation, can minimize delays.
- Regulatory compliance: Ensuring staff are aware of relevant regulations can prevent compliance issues and enhance competitive advantage.
Creating a culture of awareness around warranty management can lead to better accountability and efficiency. Regular workshops or updates can reinforce knowledge and keep the team aligned with best practices.
Investing in training and documentation pays dividends in effective warranty management.
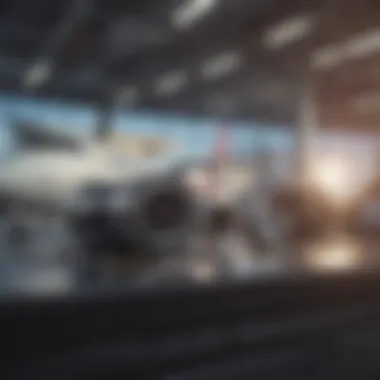
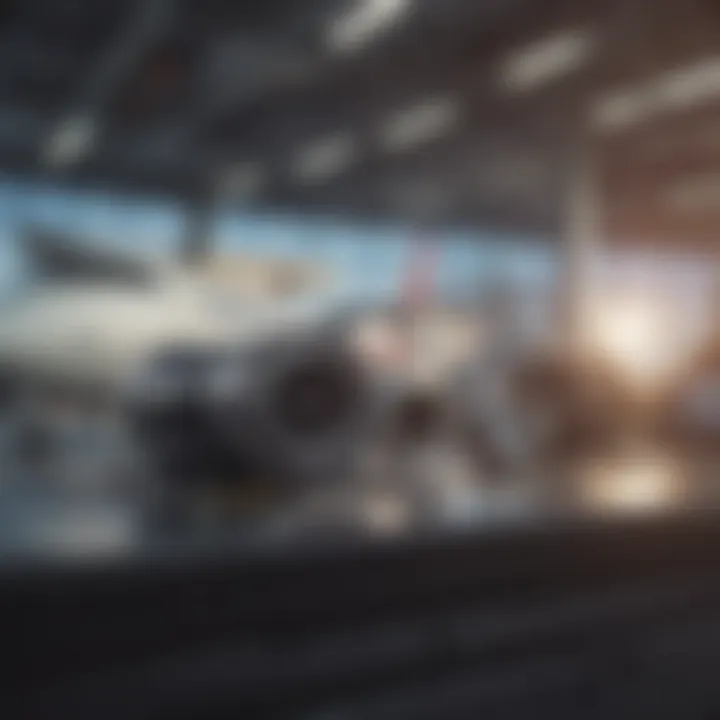
By incorporating these practices, airport operators can navigate warranty complexities with greater accuracy and foresight, leading to optimized maintenance strategies and less unplanned downtime.
Impact of Warranty Management on Operational Efficiency
Effective warranty management is critical in aviation. With the numerous components involved in airport operations, managing warranties can lead to substantial operational efficiencies. Without effective strategies in place, costs can soar, and equipment reliability may suffer. Therefore, a focused approach towards warranty management presents several advantages.
Cost Implications
Financial aspects of warranty management play a significant role in overall airport operations. Managing warranties efficiently can decrease unexpected costs and maintenance expenses. By ensuring that all equipment, from baggage handling systems to passenger boarding bridges, is covered under warranty, airports can reduce the financial burden caused by emergency repairs. Moreover, providers may offer incentives for maintenance adherence, leading to even more savings.
Some financial considerations include:
- Direct Cost Savings: Reducing repair costs through warranty claims can directly improve budget allocations.
- Predictable Budgeting: Knowing what is covered allows better forecasting of expenditures, facilitating more accurate financial planning.
- Long-Term Investments: Effective warranties can extend equipment life, ensuring that investments yield maximum returns, lowering the need for frequent purchases.
As airports modernize, the financial implications of warranties should be analyzed regularly to glean benefits from these agreements.
Maintenance and Downtime
Downtime can disrupt airport operations, leading to lost revenue and customer dissatisfaction. Warranty management can substantially ease this problem. When appliances fail, fast access to warranty claims can minimize downtime and expedite repairs. Consistent maintenance under warranty conditions might also extend the lifespan of equipment, yielding a better return on investment.
Factors regarding maintenance and downtime impacts include:
- Reduced Downtime: Quick repair processes facilitated by warranty coverage can allow airports to operate smoothly, decreasing delays in flights and improving traveler satisfaction.
- Structured Maintenance: Many warranties require routine maintenance. Implementing this proactively can greatly lower the risk of unexpected equipment failures.
- Operational Reliability: A reliable fleet of airport appliances ensures uninterrupted service, which is crucial for the overall airport experience.
Case Studies: Successful Warranty Management
Successful warranty management is critical for airport operators. In a field where equipment reliability impacts safety and efficiency, learning from existing case studies serves as an essential guideline for best practices. By analyzing how leading airports navigate warranty management, other facilities can adopt strategies that reinforce their operational frameworks, minimize costs, and enhance service efficiency.
Leading Airports' Strategies
Several prominent airports have established effective warranty management strategies. These strategies typically include regular audits of equipment performance and warranty utilization. For instance, Denver International Airport employs a systematic approach by reviewing warranty claims quarterly. This allows them to track trends and identify which appliances frequently require repair under warranty.
- Proactive Maintenance: Airports like Singapore Changi focus on proactive equipment maintenance. They not only comply with warranty requirements but also incorporate advanced analytics. This helps in predicting failures before they happen, potentially saving costs associated with equipment downtime.
- Vendor Relationships: Successful airports also cultivate robust relationships with suppliers and manufacturers. Toronto Pearson International Airport has developed partnership agreements that extend beyond the basic warranty, ensuring that they receive timely service and support.
Such approaches not only improve service reliability but also foster a culture of accountability with vendors. These strategies offer a structural framework for other airports aiming to enhance their warranty management practices.
Lessons Learned
Examining the narratives of successful airports provides valuable insights. Some common lessons emerge from these case studies that can benefit other airport operators.
- Importance of Documentation: Adequate record-keeping is paramount. Keeping detailed logs of all maintenance and repairs ensures that warranty claims can be supported with the necessary documentation.
- Training Staff: Educating staff on warranty provisions prevents misuse of warranty claims. When employees understand the best practices for equipment use and care, it reduces accidental damages that might void warranties.
- Regular Reviews: Consistent review processes are necessary. Airports should routinely assess warranty claims alongside operational reports. This not only aids in identifying recurring issues but also adjusts strategies to cope with them, thus optimizing performance.
Culmination: Navigating Airport Appliance Warranties
Understanding airport appliance warranties is critical for various stakeholders in the aviation sector. This article has dissected the layers surrounding these warranties, from their historical context to practical implementations. The significance of airport appliance warranties cannot be overstated as they safeguard investments and ensure operational efficiency.
One crucial element discussed is the regulatory framework. Comprehension of legal obligations allows airport managers and operators to navigate complex compliance requirements. This knowledge is vital as it minimizes risks associated with warranty claims, thereby enhancing financial management.
Moreover, effective warranty management practices, as detailed in previous sections, directly correlate with operational performance. By maintaining precise records, employing thorough training, and fostering awareness regarding warranties, airports can mitigate the impact of equipment failure. Ultimately, this leads to reduced downtime and associated costs, which is a priority for any operational entity.
The insights shared throughout this article serve as a guide for making informed decisions regarding airport appliance warranties. The evolving landscape of the aviation industry necessitates a proactive approach to warranty management. As technology advances, understanding future prospects will provide a competitive edge for airport operators.
“In the world of aviation, effective warranty management is not just a safeguard but a strategic advantage.”
When considering the future, the adoption of digital tools and data analytics is likely to revolutionize warranty claim processes. Increasing efficiency and enhancing accountability will become essential in managing warranties effectively.
In summary, navigating airport appliance warranties is not merely a bureaucratic necessity; it is an integral component of successful airport operations that ensures both resilience and sustainability in the aviation sector.
Future Prospects of Warranties in Aviation
The landscape of airport appliance warranties is changing as new technology emerges. Stakeholders should take note of this shift. Future warranties are expected to integrate advanced manufacturing techniques and smart technologies. These innovations could lead to warranties that are more tailored to specific equipment needs.
Anticipated future developments include:
- Enhanced Digital Tracking: Improved tracking mechanisms to manage warranty claims in real time.
- Predictive Maintenance: Utilizing big data analytics to foresee potential equipment failures and consequently optimize warranty coverage.
- Customized Policies: The shift towards bespoke warranty policies that adapt to individual airport requirements, allowing for more flexibility in coverage.
The importance of keeping abreast with these trends cannot be overstated. As technology advances, the tools available for managing warranties will become more sophisticated, addressing the needs of modern aviation with greater efficacy.